A Quiet Force with Powerful Purpose
They aren’t just about opening and closing pathways. Valves control pressure, direct flow, and safeguard systems under intense conditions. In environments dealing with high temperatures, corrosive chemicals, or volatile gases, valves act as both protectors and regulators—ensuring that every process runs smoothly, reliably, and safely.
Take a pressure relief valve as an example. In power generation facilities, this single component prevents dangerous build-up by automatically releasing excess pressure. A check valve, on the other hand, quietly stops fluid from flowing in the wrong direction—crucial in pumping stations and water supply networks.
Adapting to Every Industry, Every Condition
Different industries present different challenges—and valves rise to meet each one. In chemical processing, materials must withstand corrosion. In marine engineering, they must function under extreme pressure and resist saltwater degradation. In pharmaceutical manufacturing, cleanliness and precision are paramount.
This is where the diversity of valve types comes into play:
- Gate valves are often used for isolation in water systems.
- Globe valves provide finer control over flow, ideal for HVAC and dosing applications.
- Ball valves deliver quick shutoff, especially useful in gas pipelines.
- Butterfly valves offer lightweight, compact solutions for large diameter pipes.
- Check valves ensure one-way flow, preventing damage from reverse currents.
- Safety and relief valves act as final failsafes in pressurized systems.
- Needle valves provide pinpoint control in small, high-precision systems.
- Balancing valves maintain hydraulic equilibrium in heating or cooling loops.
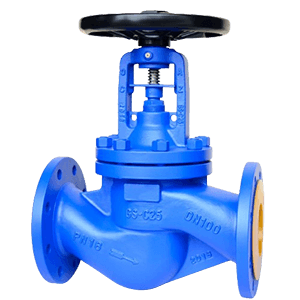
Behind Every Reliable System Is a Reliable Valve
A smooth-running facility isn’t just about automation or advanced software. It’s about hardware—valves built to endure and perform under stress. Their contribution is twofold: they increase operational efficiency and reduce risks.
Think of a factory that deals with flammable gases. Without proper valves, the margin for error narrows dangerously. But with the right valves in place—selected for material compatibility, rated pressure, and thermal limits—operators can rest assured the system is both safe and efficient.
Moreover, valves designed with low pressure drops, minimal maintenance needs, and long service life are critical for industries seeking to lower costs and environmental impact.
Selecting the Right Valve: An Investment in Stability
Valves are not one-size-fits-all. Engineers must account for:
- Media characteristics (viscous, clean, toxic, etc.)
- Pressure and temperature conditions
- Required level of flow control
- Maintenance access and frequency
- Industry-specific regulations and certifications
In short, choosing the right valve is an engineering decision that directly impacts performance, safety, and ROI. Stainless steel valves might be optimal in corrosive environments, while ductile iron may suffice for general waterworks. For critical operations, smart valves with feedback sensors and remote actuation might be the key to next-level control.
Looking Ahead: The Smart Valve Era
As industrial systems evolve, so do valves. With the rise of smart factories and IoT integration, intelligent valve systems are becoming more prevalent. These advanced units offer real-time data on temperature, flow rate, and pressure—allowing operators to make proactive decisions, avoid failures, and streamline maintenance.In this era, the importance of valves is not diminishing—it’s growing.